Grand Challenges
This Platform has been curated to connect technology seekers with technology providers. The developmental challenges of the State in key priorities sectors and unmet needs of industry requiring technological solutions are being mapped after holding interactive discussions with concerned administrative departments of the State as well as Industries/Industrial Associations.
Bicycle Industry
- Largest Cluster of Bicycle Manufacturing Industry in India with more than 90% bicycle parts manufactured in Punjab.
- 75% share in India Bicycle Production
Technological upgradation and R&D Interventions required
- Light weight & strong aluminum frame design
- Gear shifters & gears: The Indian industry has not been very successful in manufacturing efficient gear shifters and more than 90% demand is met by Japanese companies
- Disc brakes: These are also being supplied by foreign companies
- High end suspension systems
- Related tooling: Manufacturing of tools related to manufacturing & fitting of gear shifters, gears
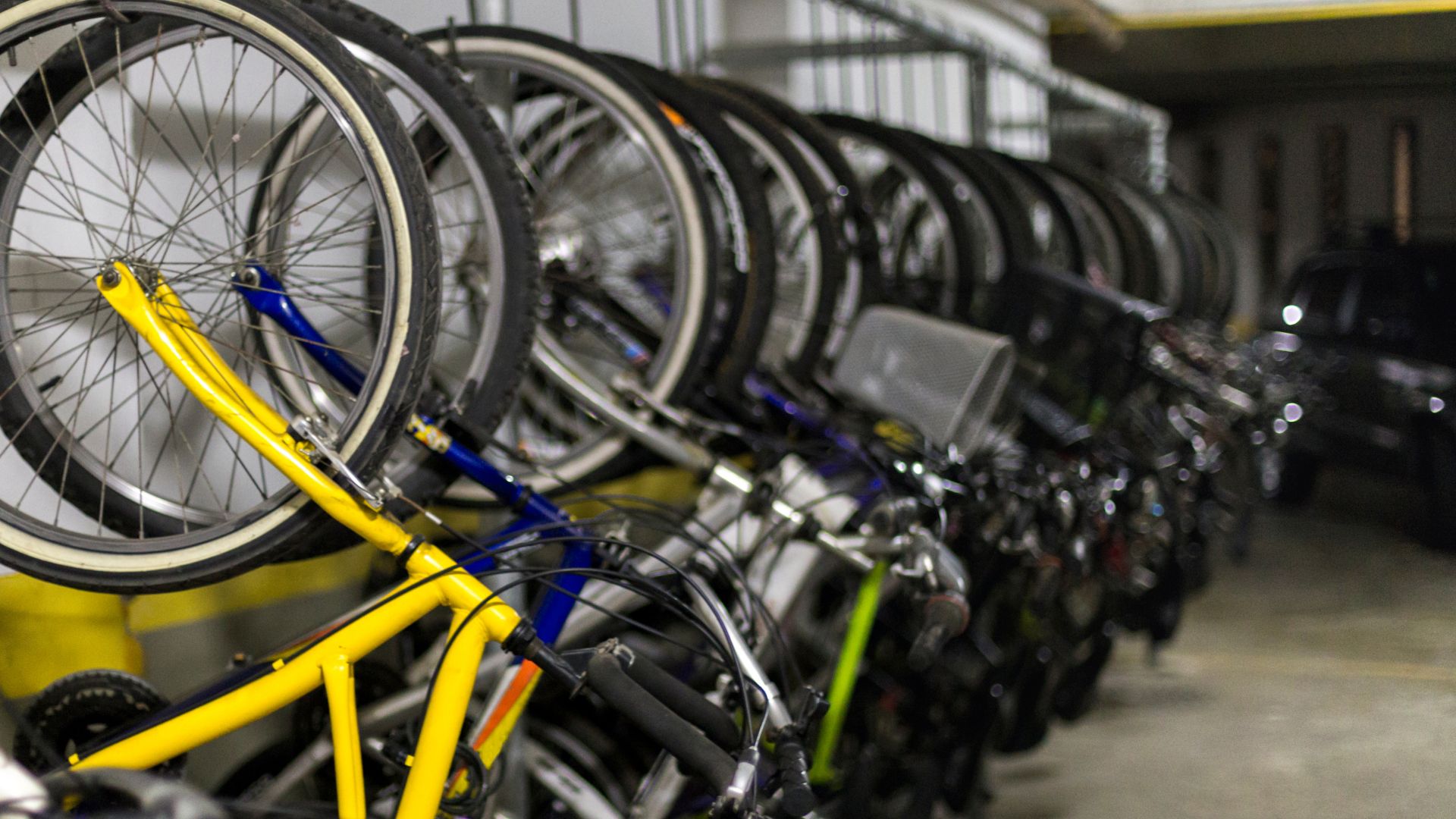
Forging Cluster
- Around 300 Forging units operating in the State
- Annual forging of 1.50 million tons of alloy steel
- Consumption of around 300 million liters of petroleum products as furnace fuel (equivalent to 9 lakh tones of CO2 emission worth Rs. 1350 Cr)
- Usage of age old technologies with very low thermal efficiency in the range of 8-20%.
- Estimated financial loss of Rs.450 crore per annum
Technological upgradation and R&D Interventions required
- Oil Heating Pumping Filtration (HPF) Unit
- Waste Heat Recovery System (WHR)
- Automation
- Refractory & Insulation
- Energy Efficient Burners
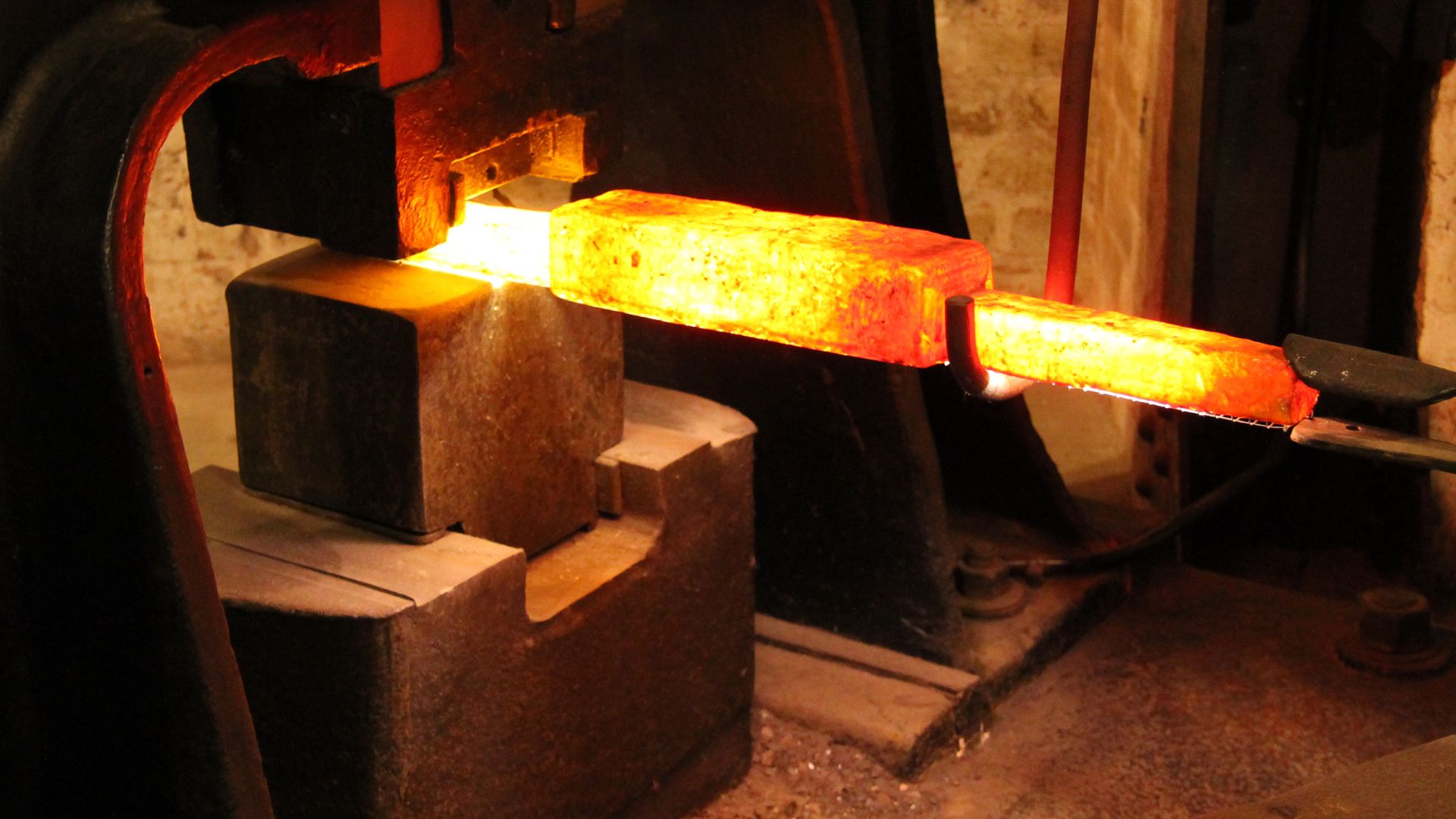
Textile & Dyeing Industry
- Punjab has 4 Textile Parks having state-of-the-art infrastructure
- Around 260 textile & dyeing industries operational in Ludhiana
Technological upgradation and R&D Interventions required
- Technical Textiles
- R&D on indigenous development of specialty fibers
- High Technology Polymers for increased used in Agro/Medical/Sports Textile etc.
- Effluent Management
- R&D and technology for new products development
- Need for technology up-gradation
- Innovations in Machinery
- Need for labs for testing of products
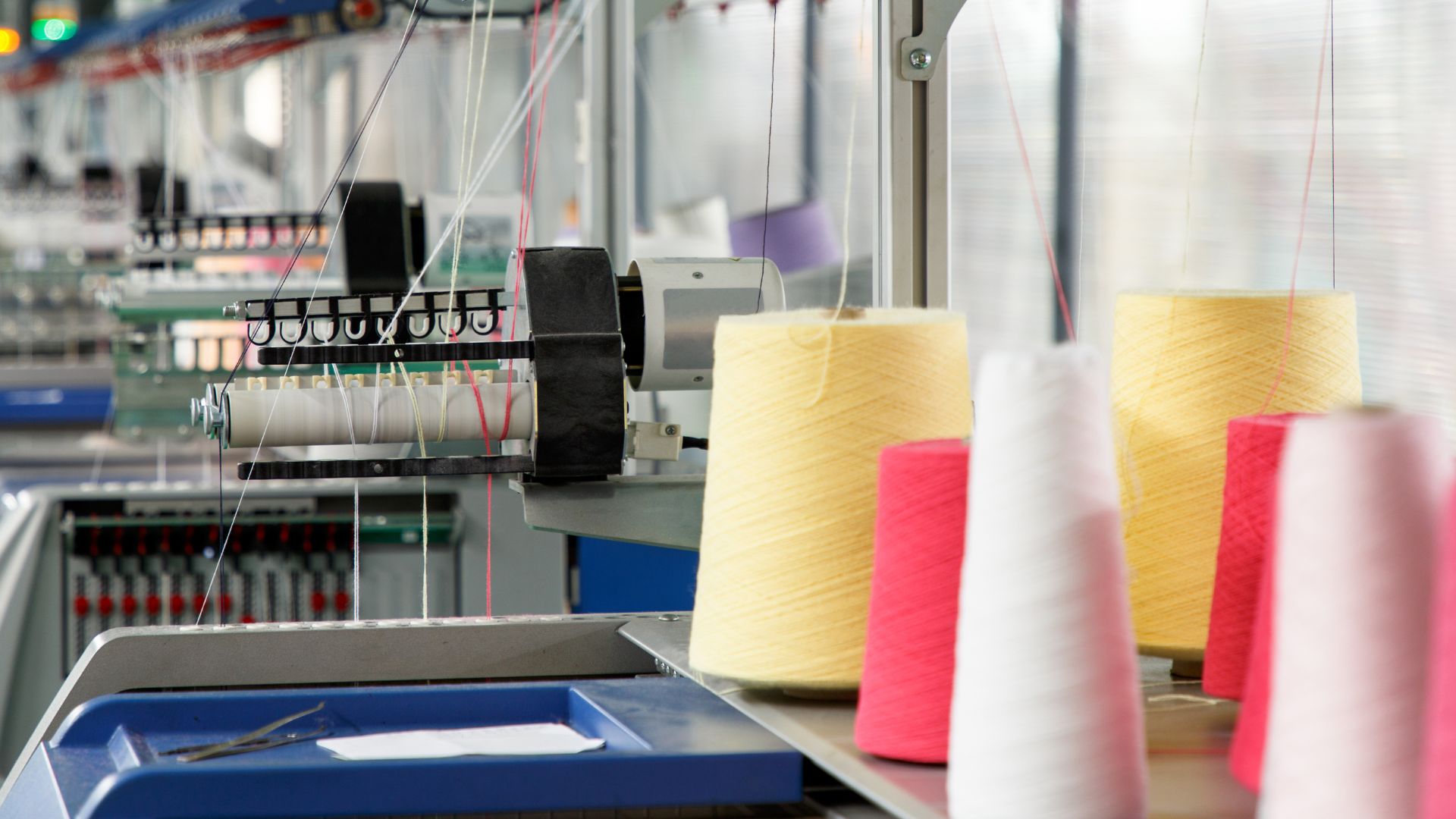
Brick Industrial Cluster
- Around 2400 brick kilns producing 1440 crores of solid clay bricks annually using coal as fuel for baking of bricks
- Annual turnover of more than Rs. 8640 crores
- Annual coal consumption of brick sector is 21.6 lakh tones (47.5 lakh tones equivalent CO2 emissions) amounting to Rs. 3110 crores
- Consumption of 2.62 lakh cubic meters of top fertile soil annually
Technological upgradation and R&D Interventions required
- Setting up of common facility center for brick sector for carrying out R&D studies, clay testing laboratory, demonstration of state-of-art technology for brick manufacturing and firing.
- Facilitation w.r.t. setting up of Resource Efficient Brick manufacturing units and related REB manufacturing machinery.
- Support w.r.t. machinery for clay brick extrusion, there being no machinery manufacturer in Punjab and lack of technical support for importing the machinery.
- Pneumatic fuel feeding system for existing high draft kiln technology which can reduce fuel consumption & improve brick quality.
- Initial firing in brick kilns using Gas/LPG in place of fire wood - to reduce emissions and improve brick quality.
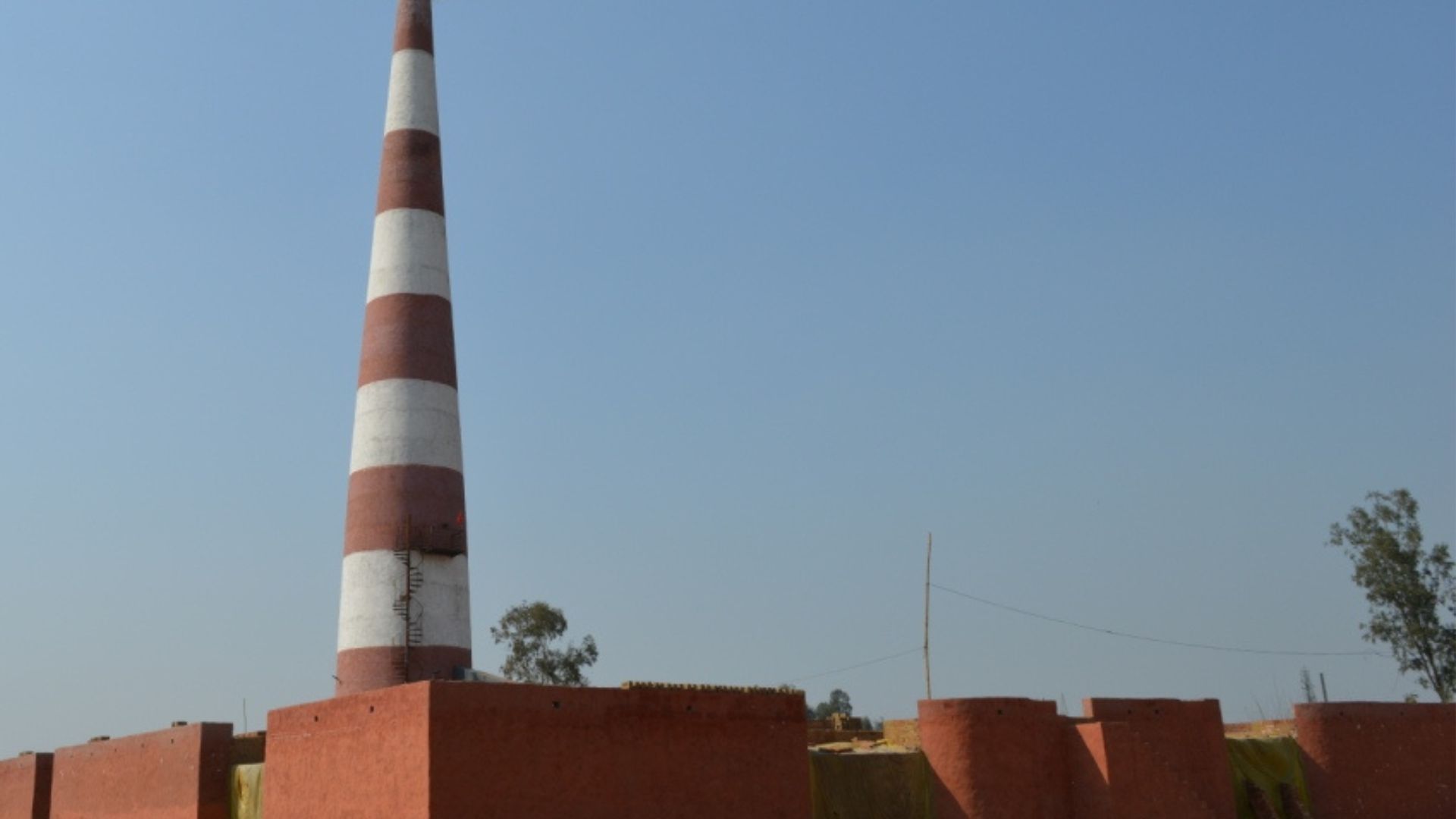
Steel Re-rolling Cluster
- Operating steel rerolling mills in the State with installed production capacity of around 45 lakh tones (worth Rs. 22500 crores) per annum
- Consumption of 2.70 lakh ton coal as fuel (worth Rs. 486 crores) generating 7.42 lakh ton of CO2 and 450 lakh ton SPM into the atmosphere
- Loss of around Rs. 450 crores per annum in the form of steel burning loss due to process inefficiencies.
Technological Interventions required
- Energy efficient reheating furnace
- Waste Heat Recovery system
- Automation & Control
- Refractory & Insulation
- Piping & combustion equipments
- Fuel preparation/handling/injection system
- Mill cooling system
- House keeping practices
- Electrical facilities monitoring & maintenance
- Roll pass design
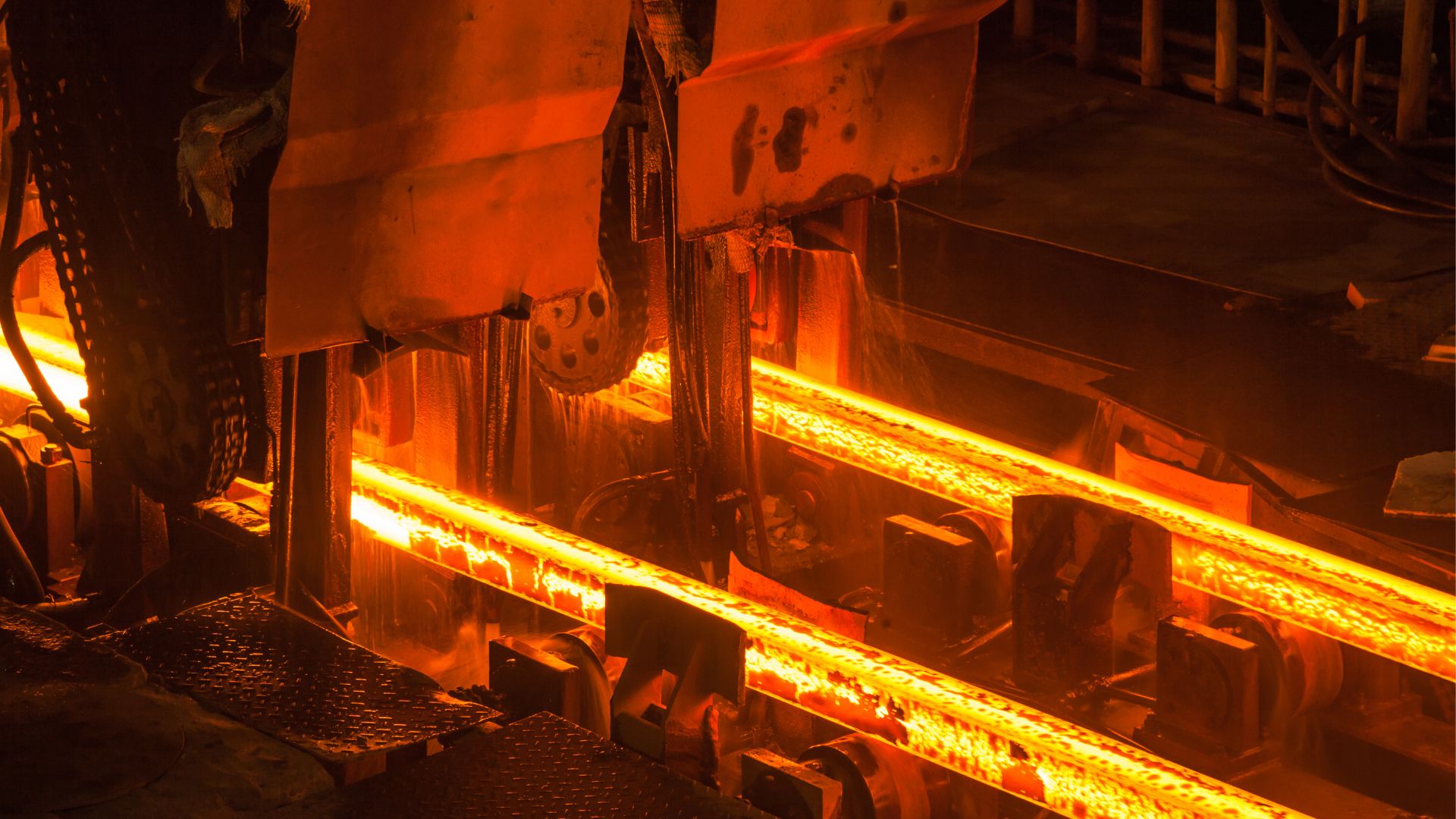
Foundry Cluster
- Around 900-1000 cupola furnaces in operation for the production of cast iron castings
- Consumption of around 78750 tons of coke worth Rs. 196 crore annually and generate 700 tons of SPM and 2.3 lakh tons of CO2
Technological upgradation and R&D Interventions required
- Setting up of testing labs/R&D centers for providing solution in casting defects, introducing casting quality improvement techniques such as Product Process Search analysis (PPS) Inspection method, Design of Experiment (DOE), using a Casting simulation software etc.
- Setting up of Common facilities with high pressure molding line, modern cold box core shop, robotized fettling etc.
- Promoting adoption of greener engineering processes like sand reclamation.
- R&D for slag utilization in construction sector.
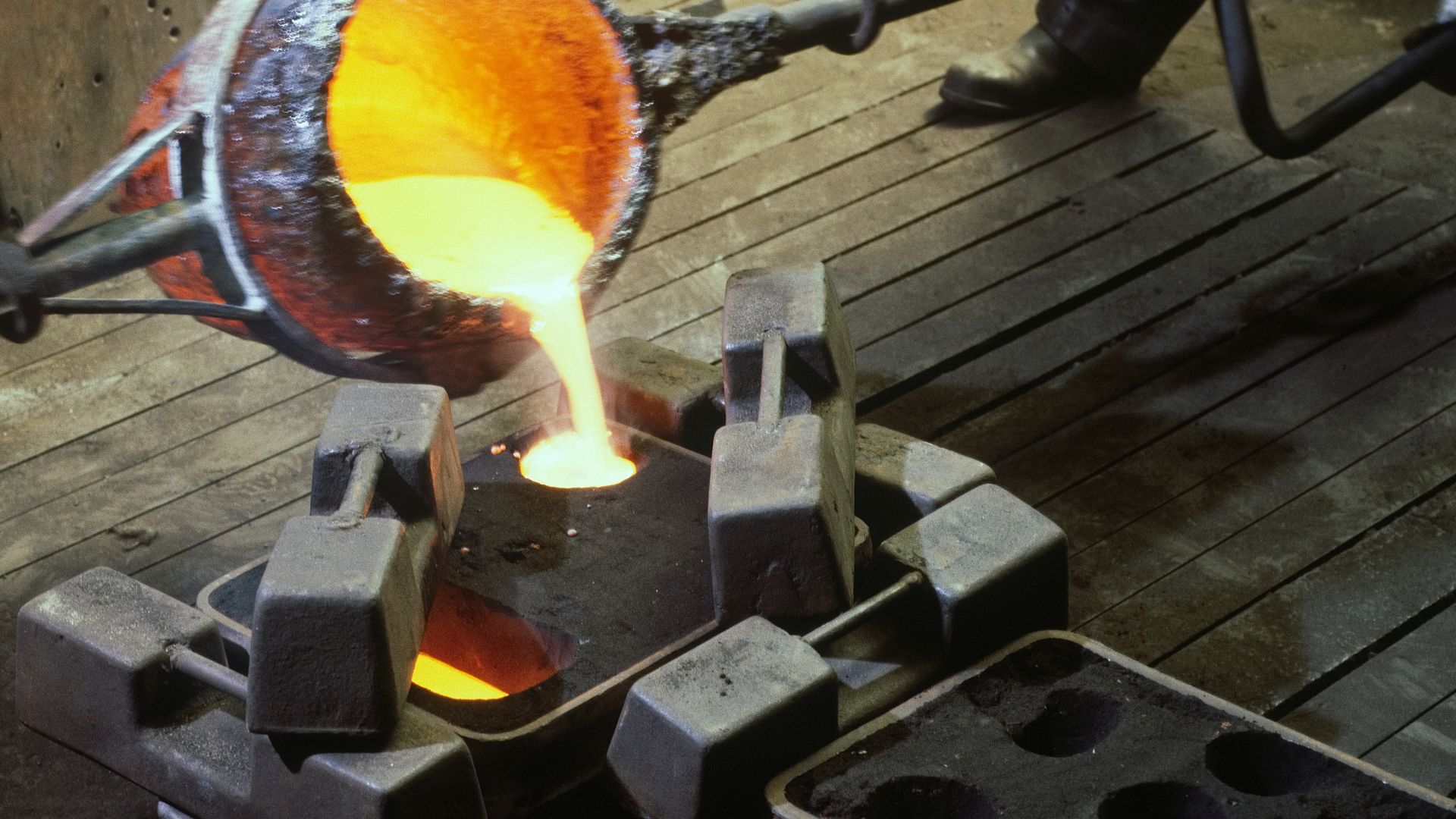
Agriculture Implements
Highest per capita agriculture implements in India
- R&D on upgrading metallurgy of wearable parts so as to compete with international companies
- Highest per capita agriculture implements in India
- A Common Facility Center (CFC) to provide access to the industry to high-end technologies like laser cutting which requires high precision.
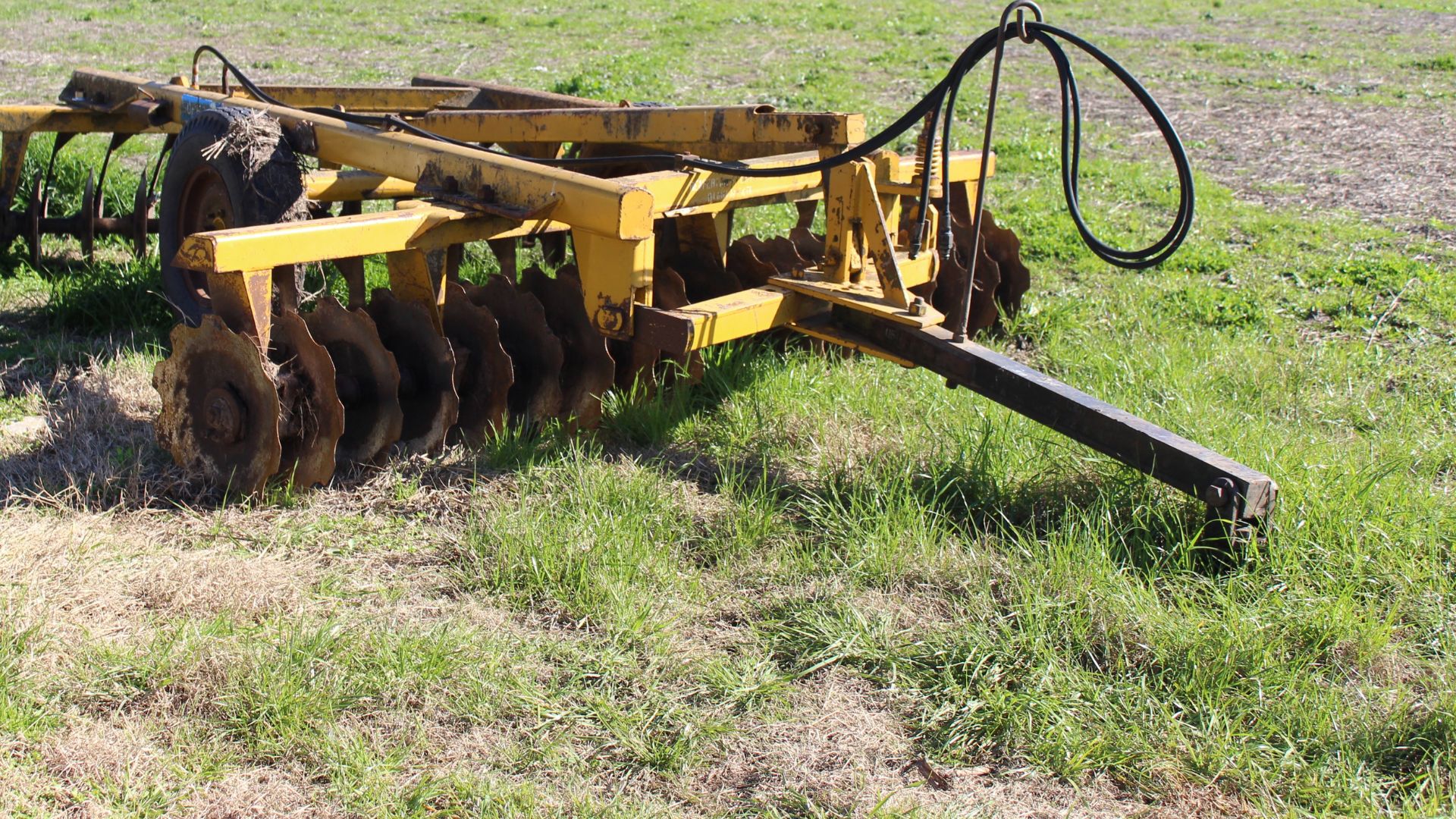
Leather Industries
Technological Interventions required
- Low cost technology for chromeless tanning
- Chemical free dehairing operations & limited salt consumption/ preservation
- Laser cutting machinery for Leather Industry
- Computer aided design
- Bio based leather
- Effluent Management
- Biogass generation from tannery solid waste
- Use of sustainable alternative of leather viz. cork, tree bark, pineapple, leaf fibers, recycled rubber leather etc.
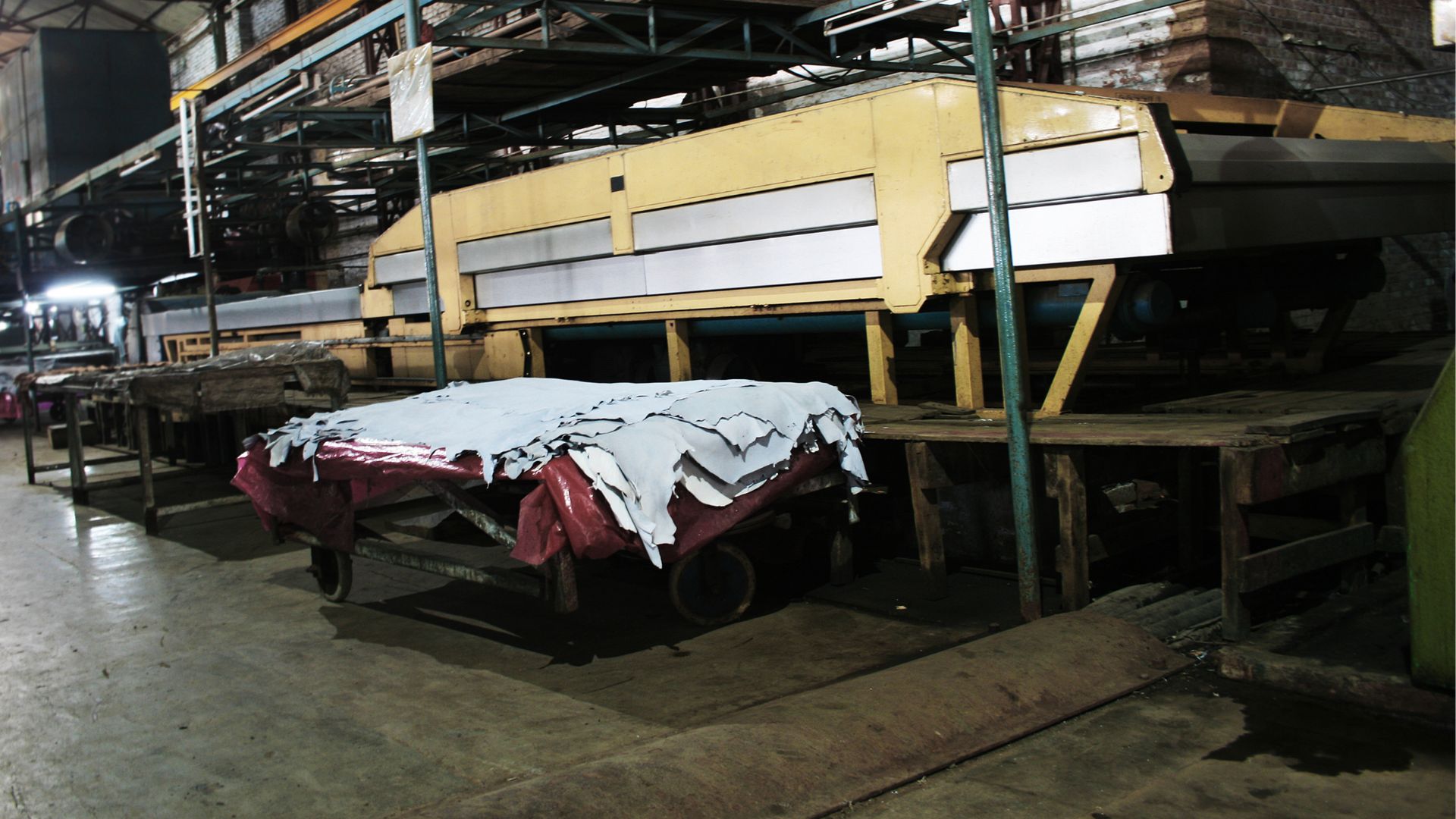
Sports Goods Sector
Jalandhar: One of the largest manufacturer of sports goods in India.
- Nano-based solutions for an added advantage such as high strength and stiffness, durability, reduced weight, abrasion resistance, etc. in sporting equipment
- Automation
- Value addition/Recycle of waste generated by Sports Industry
- Sports goods stitching Tools & Machinery
- Raw material: Presently the Industry is not getting good quality raw material locally like leather, PU/PVC. High quality PU/PVC is being imported from Korea and there is a need of locally manufactured PU/PVC.
- Absence of technology centres/ experts: No exclusive R&D centre or institute for the sector in the region, for material testing & reverse engineering services, etc.
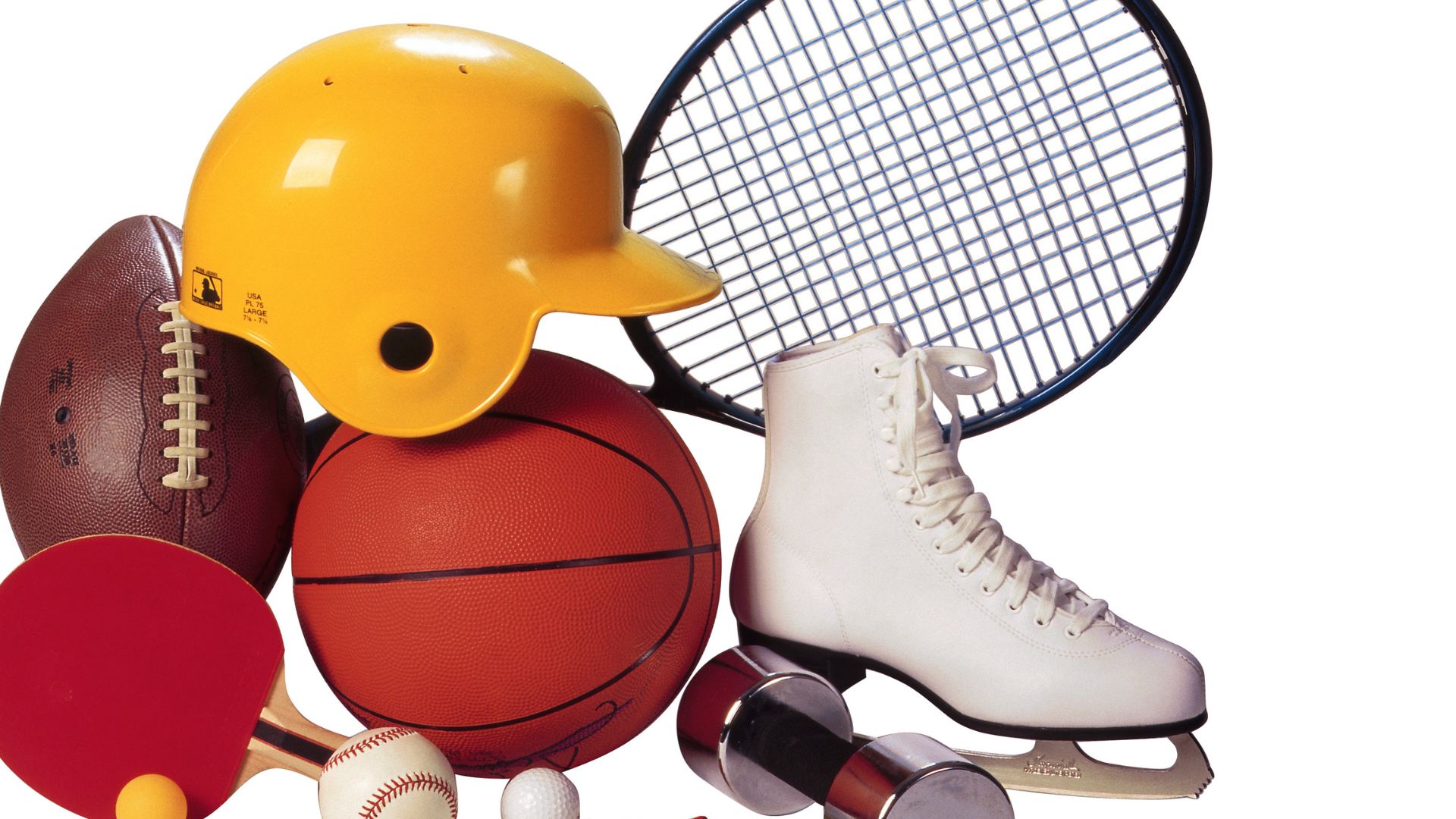
Page Under Development !